WMS Integration
Allowing your software to reach new markets can be a problem when each new marketplace requires a dedicated effort to allow your product to interact.
You know that your WMS can shine alongside many different products and product ecosystems. But how do you allow your product to interact with new systems without going through a prolonged integration effort targeting each new system?
We can help!
The LINK® manages all your integrations with a single software standard. This means standardized methodologies, standardized capabilities, and standardized support for all of your customers.
The LINK is the best choice for all of your customer’s Warehouse Management System (WMS) integration needs!
Labor Data Collection
Labor data collection is often not handled by Warehouse Management systems – as well as third-party systems. Get more out of your WMS by integrating with third-party labor data collection systems:
– Synchronize orders and route information between systems in real-time
– Synchronize employees between systems in real-time
– Automatically flow transactions as they happen: Labor data PICK/Consumption transactions; Material PICK/Consumption transactions; Production transactions
– Synchronize and utilize piece-rate, labor-rate or other data stored in your ERP
The LINK automatically synchronizes data between the two systems, on a schedule or in real-time (when allowed). The labor data tracking system always has the latest orders, routes, employees, and related data without the need for manual intervention. System-optimized adapters ensure connectivity to a wide variety of systems.
Time & Attendance/Payroll
Time & Attendance/Payroll Integration may not seem like an obvious integration play for WMS, but capturing worker data per order, per operation, per shift, (and team data as well) are all valuable data segments for WMS. With The LINK you will:
– Synchronize employees and employee data
– Start/Stop worker or team shifts based on WMS events
– Send work record transactions based on WMS events
MES Systems
MES Systems can be a great adjunct to a WMS system, but only if you have a good integration strategy.
MES to and from WMS integration can be achieved using several different strategies, most involving an ERP system and ERP integration. But you can also make MES and WMS work together directly by integrating the core data required of each system.
MES to and from WMS
Note that each of these integration maps can run in either direction depending on which system “owns” the initial data:
– Items, UOM, and related data
– Inventory transactions / levels
– Production Orders
MES to WMS
These maps flow directly from MES to WMS:
– Consumption (of raw materials or labor)
– Production (Production order receipts)
The LINK synchronizes data between the MES and WMS automatically. Transactions in one system flow seamlessly to the next, allowing workers to move from system to system without having to wait or perform manual transactions to sync the systems.
ERP Systems
ERP Systems are at the core of every manufacturing facility. They handle supply and demand and, in many cases, inventory, scheduling, and more.
ERPs in a WMS environment need to be updated regularly (ideally in real-time) with production order activities.
ERP to WMS
– Items, UOM, and related data
– Inventory transactions / levels
– Purchase Orders
– Sales Orders
WMS to ERP
– Shipments
– Purchase Order Receipts
– Inventory Adjustments / Transfers
The LINK synchronizes data between the ERP and the WMS automatically. Transactions in one system flow seamlessly to the next, allowing workers to move from system to system without having to wait or perform manual transactions to sync the systems.
Alerts
Alerts are often lacking in Warehouse Management Systems. With The LINK you can add alerts for a wide variety of scenarios including customized alerts to suit just about any situation:
– Item entry is missing data (like costs or other ties) XX hours after a new item is entered
– Production/Consumption milestones
– Inventory level / Kanban alerts
– Real-time alerting for parts sent to quarantine, or specific areas
– Alerting on shipment activities (on what is being shipped, or even on what is not being shipped though user-customizable rules)
– User-configurable
The LINK has support for custom criteria so no matter what the alert criteria is – if they can describe it, then TheLINK can probably support it. Alerts can be stored in the database (for reporting) and/or go out as emails or text messages. Alerts are in real-time – just like you expect them to be.
Leverage enterprise-class integration capabilities:
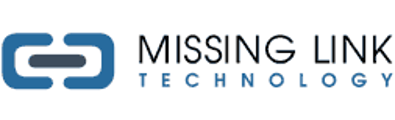
Missing Link Technology has deep domain knowledge of ERP and manufacturing as well as integration experience with dozens of ERP and other manufacturing systems. You can leverage best-of-breed solutions to work with your WMS system by using The LINK® for seamless integration between all systems.